Какие химические свойства у чугуна
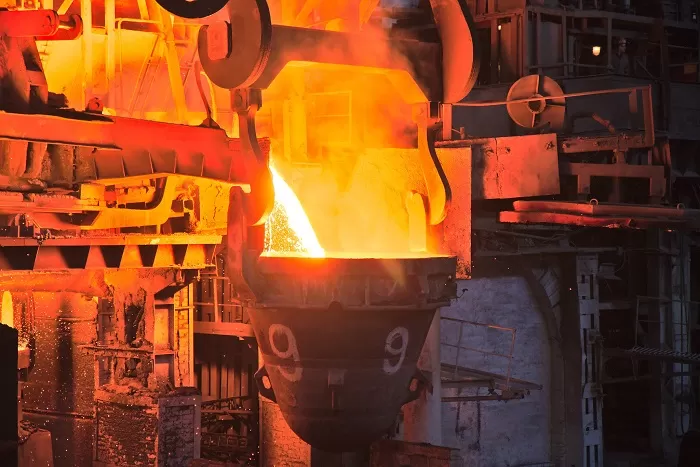
Люди научились получать чугун еще несколько веков назад, и по сей день он остается одним из наиболее востребованных материалов. Уникальные свойства чугуна позволяют использовать его в быту и в самых разных сферах деятельности. Так чем же примечателен этот металл, и почему он так популярен?
Общее описание
Чугунные сплавы, как и стальные, состоят из железа и углерода. Функция углерода, в данном случае, заключается в придании металлу твердости и прочности. Но в отличие от стали, содержащей не более 2% углерода, чугунные сплавы им более насыщены. Максимальное содержание углерода в чугуне может достигать 6%. Но на практике используются соединения, содержащие 3%-3,5% этого вещества.
Благодаря насыщению углеродом этот сплав обретает высокую прочность и твердость. Но эти же качества придают чугуну хрупкость. Чугунные изделия не выдерживают ударных нагрузок. При ударах они трескаются. Поэтому этот металл не поддается никаким видам обработки, кроме литья. Все изделия, включая детали для машин, посуду и предметы интерьера, отливаются.
Виды сплавов
Углерод в чугунах может содержаться в двух видах:
- в виде цементита – химического соединения;
- в виде графита – природного минерала, являющегося аналогом углерода.
Цементит придает сплаву белый цвет, а графит – серый. За счет такой особенности выделяют две разновидности чугунов – белый и серый. Серый чугун содержит крупные включения графита, которые значительно повышают его хрупкость.
Применение белой разновидности очень ограничено. Из-за чрезмерной твердости и хрупкости он плохо поддается резке. Поэтому чаще всего его используют для создания поверхностного слоя, требующего повышенной твердости. Также из белого чугунного соединения отливают шары, предназначенные для перемалывания промышленного сырья.
Графит добавляет материалу пластичности. Но серая разновидность содержит больше вредных примесей в виде серы и фосфора, от которых не удается избавиться в процессе производства.
С целью повышения пластичности чугуна и снижения его хрупкости в сплавы добавляют магний и церий. С помощью эти веществ удается изменить форму графита и, соответственно, устранить хрупкость металла. В результате производители получают высокопрочный чугун, качество которого не уступает стали.
Также современные методы производства позволяют получить ковкий чугун и легированный. Название первой модификации не указывает на возможность обработки металла методом ковки. Оно лишь указывает на высокую прочность, пластичность и вязкость сплава.
Легирующие соединения обладают улучшенными свойствами, так как в их состав вводятся легирующие компоненты, оказывающие положительное влияние на структуру, форму и размеры включений углерода.
Химический состав
Химической формулы чугуна не существует, так как это не отдельное вещество, а сплав двух и более веществ. В состав чугуна входят следующие компоненты:
- железо (Fe) – основа сплава;
- углерод (C);
- кремний (Si);
- марганец (Mn);
- фосфор (P);
- сера (S);
- хром (Cr);
- никель (Ni);
- молибден (Mo).
Железо и углерод – это основные компоненты сплава.
Кремний – второй по важности элемент после углерода. Он увеличивает жидкотекучесть, делая материал более мягким. За счет добавления кремния удается улучшить его литейные качества. Марганец повышает прочность сплава.
Сера и фосфор – вредные примеси, от которых не удается избавиться в процессе производства. Увеличение содержания серы и фосфора ухудшает жидкотекучесть металла и приводит к образованию трещин в отливках.
Остальные компоненты добавляются с целью придания металлу большей прочности, износостойкости, жаропрочности. Они повышают устойчивость материала к сухой и влажной коррозии, а также к воздействию агрессивных сред.
Количество легирующих компонентов определяет степень легированности чугуна. В зависимости от этих показателей выделяют следующие виды чугунных сплавов:
- низколегированные, в которых содержится не более 2,5% дополнительных компонентов;
- среднелегированные (не более 10%);
- высоколегированные (более 10%).
Хотя стоимость легированных чугунных соединений значительно ниже, чем у нержавеющих сталей, изделия из них получаются прочными и качественными.
Физико-механические свойства
Плотность чугуна | 6,6-7,8 г/см3 |
Температура плавления | 1200°С |
Удельная теплоемкость | 500 Дж/кг |
Теплопроводность | 58 Вт (м*К) |
Термический коэффициент линейного расширения | 10,4 |
Твердость | 7,5 баллов по шкале Мооса |
Модуль упругости | От 8000 для серых типов От 17000 для высокопрочных |
Предел прочности при растяжении | 370-630 Н/мм2 |
Ударная вязкость | 0,01-0,04 МДж/м |
Улучшение физических свойств чугуна достигается за счет добавления ванадия и молибдена. Увеличить прочность позволяют марганец и кремний. Хотя количество каждой примеси в сплаве не превышает 1%, за счет их добавления удается увеличить вязкость сплава, уменьшив его хрупкость.
Плотность чугуна в кг/м3 колеблется в пределах 6600-7800. То есть он легче стали, но значительно прочнее. Этот фактор объясняется его твердостью, которая всего на 2,5 балла ниже, чем у алмаза.
Тепловые свойства
Свойства чугуна при нагревании изменяются. Тепловые характеристики зависят от состава сплава. Показатель теплоемкости зависит от наличия легирующих компонентов, а также интенсивности нагрева материала – чем она выше, тем больше теплоемкость. Удельная теплоемкость чугуна соответствует следующим значениям:
- в твердом состоянии – 1 кал/см3;
- в расплавленном виде – 1,5 кал/см3.
Теплопроводность определяет, насколько материал способен проводить тепло. Значение этого показателя зависит не только от того, какие компоненты входят в состав чугуна в процентах, но и от структуры самого сплава. Для твердого материала он гораздо выше, чем для расплавленного, и варьируется в пределах 0,08-0,13 кал/см3.
Гидродинамические свойства
В зависимости от того, сколько углерода в чугуне, его вязкость может снижаться или увеличиваться. Уменьшить показатели вязкости удается за счет увеличения процентного содержания марганца, уменьшения части серы и добавления компонентов неметаллического происхождения. Вязкость увеличивается, когда температура сплава переходит в точку затвердевания.
Химические свойства
К химическим свойствам относятся способность металла к окислению и его способность сопротивляться коррозии. Для определения каждого из этих показателей огромное значение имеет то, из чего состоит чугун.
Его окисление происходит под действием кислорода и углекислого газа. Уменьшить процесс окисления при заливке сплава позволяет обработка соединениями, содержащими литий.
Степень окисления имеет огромное значение в процессе сцепление металла с грунтом. В этот момент на поверхности металла образуется окисная пленка. А при значительной степени окисления образуется легкоотделяемый слой окалины, который значительно ухудшает сцепление.
Процесс окисления чугунных соединений с шаровидным графитом происходит по-другому. Образующаяся на его поверхности пленка полностью изолирует в металлической основе включения водорода друг от друга и прекращает доступ окислителя вовнутрь сплава.
Чугун подвержен избирательной коррозии (графитации), при которой частично удаляются основные металлические фазы, а на их месте остаются графит, феррит и губчатая масса. При этом получившийся графитный слой впоследствии препятствует дальнейшей коррозии.
Степень сопротивления коррозии зависит от химического состава чугуна. Легирующие компоненты оказывают положительное влияние на структуру сплава и способны повышать сопротивляемость к коррозии. Процентное содержание углерода в чугуне не оказывает влияния на его коррозийную стойкость.
В таблице приведены примерные сведения о скорости коррозии чугуна в разных агрессивных средах.
Воздействующая среда | Потеря веса, г/м2 в день | |
Нержавеющий чугун | Серый чугун | |
Соляные и щелочные растворы | до 3,85 | 23,33-97,23 |
Кислоты | до 531 | 1,11-675 |
Вода | до 18,04 | 0,17-13,05 |
Источник
Под понятием «чугун» может подразумеваться как конструкционный материал на основе железа, так и металлический сосуд, округлый горшок для приготовления пищи. Последний попадается редко. Современная посуда теснит.
Совсем устарело слово «чугунка». Так в XIX – начале XX века называли железную дорогу.
Что такое чугун
Это сплав железа и углерода с содержанием последнего от 2,14%. В идеальном случае. На деле помимо указанных всегда есть примеси и легирующие элементы. Так что разграничение «плавает».
В зависимости от содержания углерода относительно эвтектики выделяют разновидности металла. Эвтектика – состав сплава с минимальной температурой плавления.
Для чугуна содержание углерода ориентировочно составляет 4,3%. Почему «ориентировочно» – уже говорилось. Потому принято подразделять чугун на:
доэвтектический — 2,14 — 4,3% углерода;
эвтектический — 4,3% углерода;
заэвтектический — от 4,3 до 6,67% углерода.
Виды чугуна
В общепринятой классификации разделяют по форме содержащегося углерода.
Белый
Называется так из-за характерного окраса скола. Углерод C содержится в виде цементита (формула Fe3C), образующегося при остывании расплава. Твердый тугоплавкий материал.
В доэвтектических сплавах – в составе перлита и ледебурита. В эвтектических – в ледебурите. В заэвтектических – первичный цементит и ледебурит.
В исходном виде такой чугун практически не используется. Не поддается обработке инструментом из «быстрорежущей» стали. Только с насадками из карбидов (ВК), да и то с трудом.
Применяется в качестве сырья для получения ковкого.
Серый
Также именуется по оттенку на сколе. Содержит фракции графита различной формы. Осаждению углерода способствует добавка кремния.
Свойства и структура сильно зависят от условий остывания после кристаллизации.
Быстрое охлаждение даст преобладание перлита. Сплава феррита и карбида. Своеобразная «закалка» повысит прочность и твердость. И хрупкость, что не всегда приемлемо.
Щадящее остывание определяет рост содержания феррита. Сплава железа с оксидами, в основном с Fe2O3. Улучшится пластичность. Поэтому режимы подбирают исходя из требуемых параметров.
Серый чугун удобен для литых конструкций. Отличается невысокой температурой отвердения, хорошей жидкотекучестью. Не склонен к образованию раковин.
При всем этом, углеродные вкрапления обуславливают низкую трещиностойкость. Материал уверенно воспринимает сжимающие усилия, но совершенно непригоден при растяжении/изгибе.
В маркировке указываются символы СЧ и предельная прочность в кг/мм2: СЧ25. Наиболее распространены чугуны с содержанием C ниже 3,7%.
Ковкий
Для изготовления белый чугун нагревают до нужной температуры, выдерживают достаточное время и медленно остужают («отжиг»). Процесс провоцирует процесс распада Fe3C с выделением графита и появление феррита.
По форме включения углерода не похожи на аналогичные в сером чугуне. Этим объясняется появление некоторой стойкости к разрыву и ударной вязкости.
Маркируется «КЧ» с добавлением допустимой прочности на растяжение в МПа х 10-1 и максимального относительного удлинения. Пример: КЧ 35-11.
Высокопрочный
Вид серого чугуна, только графитовые образования по форме напоминают шарики. Округлость включений делает кристаллическую решетку не склонной к образованию трещин.
В результате ценные изначально свойства чугунов (стойкость к сжатию, удобство литья и т. д.) дополняются сравнимым со сталями пределом текучести при растяжении, появляется трещиностойкость, пластичность.
Маркируются аналогично ковким, но с обозначением «ВЧ».
Передельный
Используется как сырье для выплавки стали. Часто даже не покидает предприятия, где сделан.
Специальные
Выпуск таких марок невелик, до 2% от общего объема. Могут содержать значительное количество легирующих элементов. Предназначены для ограниченных целей и специфических условий. Распространены коррозионно и химически стойкие ферросплавы.
Одна из разновидностей – антифрикционный чугун. Используется для изготовления трущихся деталей. Легируется в первую очередь хромом. Также добавляются никель, титан, медь и прочие.
Отличается высокой твердостью (до HB 300) и низким коэффициентом трения (до 0,8 при отсутствии смазывающих эмульсий).
Базовые материалы: серый, ковкий и высокопрочный чугуны. Маркировки соответственно – АЧС, АЧК, АЧВ. Цифровые составляющие описаны выше.
Достоинства и недостатки материала
Стоит обсуждать в сравнении со сталью, хотя низкокачественная углеродистая сталь – тот же чугун по сути.
По некоторым параметрам (плотность, свойство магнититься, типичные химические реакции) ферросплавы практически идентичны. Существенны отличия в технологии использования.
Преимущества:
Умеренная стоимость. Насыщение углеродом – часть процесса выплавки из руды. Снижение его содержания неизбежно удорожает металл.
Превосходные литейные качества. Расплав текуч. С низкой усадкой при кристаллизации, что минимизирует дефекты. Относительно низкая температура плавления.
Изделия прочны, с твердой поверхностью, износостойки.
Используемые в машиностроении составы поддаются обработке резанием.
Долговечны. В том числе в сантехнических, канализационных деталях.
Ставшие ненужными элементы легко утилизировать. Любой пункт приема с руками оторвет.
Недостатки:
Из-за высокого содержания углерода хрупок. Мало пригоден для обработки давлением. Из отдельных марок получают кованые изделия отменного качества. Но это скорее работа штучная и в индустриальных масштабах нерентабельная.
Сварка допускается только в крайних случаях. Технология довольно сложна, велик риск возникновения дефектов.
Изделия всегда массивны. Не получится тонкостенная конструкция, так как не выдержит собственного веса и изготовить не удастся.
Легко окисляется во влажной среде. Насквозь не проржавеет из-за неизбежной монументальности, но вид приобретет неопрятный. Детали, расположенные на открытом воздухе, нуждаются в коррозионно стойком покрытии.
Производство чугуна
Зачатки черной металлургии человек освоили уже во II-ом тысячелетии до н. э. Для получения стали. Но доменные печи появились в Европе только в XIV – XV веках. Чугун был получен как побочный ненужный продукт.
Оценили, когда обратили внимание на выдающиеся литейные качества. Удобен для изготовления пушек-ядер, да и сталь из него получать удобнее.
До России технология осмысленно дошла в XVII веке. Случилось это при Петре I, когда искали материал для оружия.
В качестве сырья обычно используются железняки. Наибольший выход получается из магнитного и красного, обильно содержащие Fe.
Для поддержания температуры используется кокс. Воздух для горения подается принудительно. Флюс (известняк) предназначен для снабжения углекислым газом. Основная реакция:
.
Восстановленное Fe опускается в горн, где насыщается углеродом. Цикл работы печи – непрерывный.
Получение стали
Порядка 85% чугуна уходит на дальнейшее изготовление стали. Для выплавки используется мартеновская печь.
В процессе плавления загруженного сырья образуется значительная масса оксида FeO. По мере разогрева происходит реакция:
.
Лишний углерод удаляется.
Также используются электродуговые и индукционные печи.
Области применения
В связи с современной тенденцией максимального облегчения оборудования, чугун используют все меньше.
Но есть области, где он пока незаменим и рентабелен:
В машиностроении применяется для крупных корпусных деталей с незначительными нагрузками на растяжение. Станины для станкового оборудования, блоки цилиндров для двигателей внутреннего сгорания. Маховики, шкивы, шестерни, гидроцилиндры, корпуса редукторов, электродвигателей, поршни.
Сантехническая фурнитура, канализационные трубы.
Декоративные элементы: ограды, решетки, ворота.
Печи для домов, бань.
Источник
Физические свойства чугуна (плотность, теплофизические и электромагнитные свойства) зависят от состава и структуры, а следовательно, от вида и марки чугуна.
Плотность чугуна.
Пренебрегав сравнительно малым влиянием ряда элементов в обычном чугуне, можно рассчитать плотность чугуна.
где С, S, Р — массовые доли элементов,%;
Сr — массовая доля графита, %;
П0 — пористость, %;
15 Ссв; 2,7 S; 14,5 (Р—0,1) — количество карбидов железа, сульфидов марганца н фосфидной эвтектики соответственно.
Приведенная формула дает вполне удовлетворительные совпадения с экспериментальными данными.
В табл. 1 приведена плотность различных групп чугунов.
Наибольшей плотностью характеризуются белые чугуны, не содержащие свободных графитовых включений, а некоторые легированные чугуны (хромовые, никелевые, хромоникелевые).
Группа чугуна | Марка чугуна | Структура | Плотность, т/м2 |
---|---|---|---|
Белый | — | Перлит, карбиды | 7,4-7,75 |
С пластинчатым графитом | СЧ15, СЧ18 | Ферритная, ферритноперлитная | 6,8-7,2 |
СЧ20-СЧ25 | Перлитная | 7,0-7,3 | |
СЧ30, СЧ35 | Перлитная | 7,2-7,4 | |
Высокопрочный с вермикулярным или шаровидным графитом | ВЧ 35-ВЧ 45 | Ферритная | 7,1-7,2 |
ВЧ 60-ВЧ 80 | Перлитная | 7,2-7,3 | |
ВЧ 100 | Бейнитная | 7,2-7,35 | |
Ковкий | КЧ 30-6/КЧ 37-12 | Ферритная | 7,2-7,24 |
КЧ 45-7/КЧ 65-3 | Перлитная | 7,3-7,5 | |
Легированный | Никелевый с 34-36% Ni | Аустенитная | 7,5-7,7 |
Никелевый с медью типа ЧН15Д7Х2 – нерезист | — | 7,4-7,6 | |
Хромовый тип ЧХ28, ЧХ32 | — | 7,3-7,6 | |
Хромово-никелевый | — | 7,6-7,8 | |
Кремнистый типа С15, С17 | Ферритная | 6,7-7,0 | |
Чугун с 12% Mn | — | 7,1-7,3 | |
Алюминиевый: с 5-8% Al типа ЧЮ22Ш – чугаль | — | 6,4-6,7 | |
Ферритная | 5,6-6,0 |
У серых чугунов плотность обычно тем больше, чем выше прочность чугуна.
Высокопрочный чугун при прочих равных условиях (одинаковом содержании кремния, перлита и графита) характеризуется большей плотностью, чем чугун с пластинчатым графитом. Однако во многих случаях эта плотность может оказаться на практике ниже, чем у серых чугунов, вследствие более высокого содержания углерода и кремния или большей ферритизации матрицы.
Большей плотностью также характеризуются аустенитные чугуны, вследствие более плотного строения, особенно при легировании никелем и мелью, плотность которых больше, чем у железа.
При легировании марганцем плотность аустенита несколько понижается. Еще меньше плотность ферритных кремнистых и алюминиевых чугунов.
Во всех случаях на плотность отливок влияет пористость (газовая, усадочная), величина которой колеблется обычно от 0,5 До 1,2% в зависимости от состава чугуна, характера кристаллизации и технологических факторов (эффективности питания, толщины стенки и т. п.), которые, в свою очередь, определяются технологичностью конструкции отливки. Наибольшее значение имеют условия питания, гидростатический напор, под которым происходит затвердевание отливки. Поэтому плотность в верхних частях крупных отливок может быть на 5% меньше, чем в нижних частях, а в центре — на 10% меньше, чем на периферии.
Плотность графитизированного чугуна уменьшается также с увеличением толщины стенки отливки вследствие увеличения степени графитизации и укрупнения графита:
Толщина стенки, мм | 10 | 12,5 | 25 | 37 |
---|---|---|---|---|
Плотность, т/м3 | 7,23 | 7,14 | 7,08 | 7,02 |
С увеличением жесткости форма Уменьшается предусадочное расширение, а следовательно, и усадочная пористость. Поэтому отливки, полученные в металлические формы, при прочих равных условиях более плотные, чем отливки, изготовленные в песчаных формах.
Источник