Какое влияние оказывает углерод на свойства сплавов
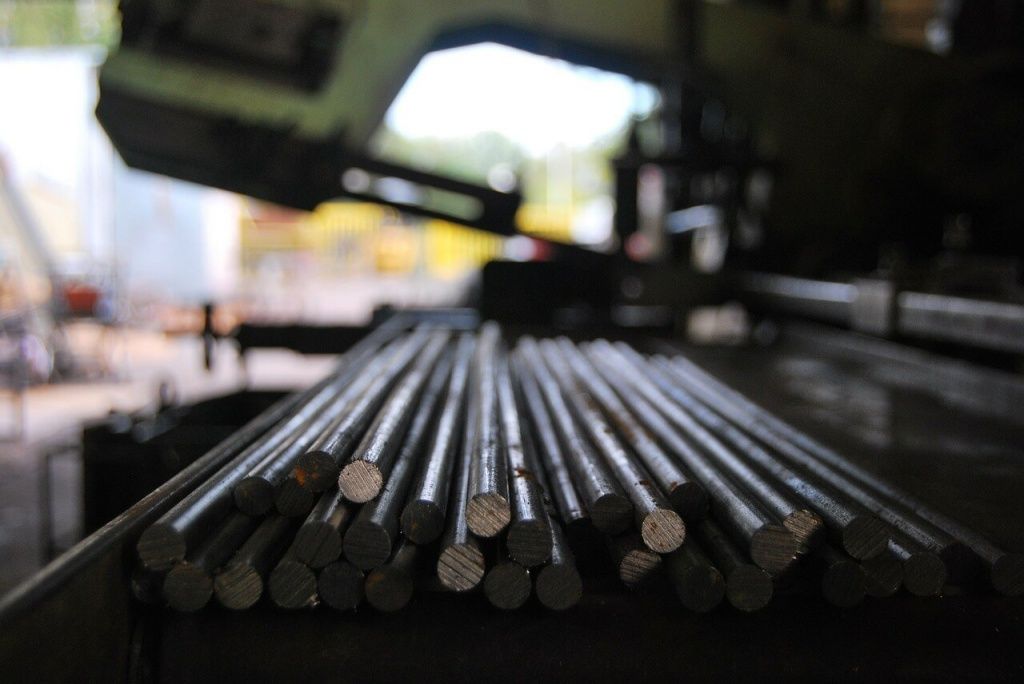
По мере повышения концентрации углерода в стали и чугуне изменяются структура и их механические свойства. Прочность горячекатаной стали в нормализованном состоянии с увеличением содержания углерода повышается, а пластичность снижается (рис. 4.4.2). Повышение прочности достигает предельного значения при содержании углерода около 0,9 %. При дальнейшем увеличении количества углерода наблюдается возрастание твердости, но снижение прочности. Это объясняется влиянием хрупкой цементитной сетки, которая окружает зерна перлита и уменьшает прочность связи между ними.
Кроме того, с увеличением содержания углерода снижаются технологические свойства стали, увеличивается усадка, ухудшается жидкотекучесть, ковкость и свариваемость, затрудняется механическая обработка. Поэтому для сварных конструкций используют стали с пониженным содержанием углерода (до 0,3 %), а штамповки изготовляют из стали с содержанием углерода до 0,5 %.
Рис. 4.4.2. Зависимость механических свойств стали от содержания углерода
Следует остановиться на влиянии формы цементита на механические свойства перлита. Частички цементита в перлите могут быть не только в виде пластинок, но и в виде округлых зерен.
Изменение формы цементита существенно изменяет механические свойства стали и прежде всего пластичность. У стали со структурой зернистого перлита предел прочности и твердости ниже на 15−20 %, чем у стали со структурой пластинчатого перлита, а относительное удлинение выше в 2−4 раза. Например, сталь с содержанием 0,8 % С со структурой пластинчатого перлита имеет предел прочности σВ = 800 МПа, относительное удлинение δ = 14 %, а со структурой зернистого перлита σВ = 590 МПа,
δ =29 %. Повышенная пластичность зернистого перлита объясняется тем, что глобулярные частицы цементита оказывают меньшее сопротивление развитию пластической деформации по сравнению с пластинчатыми. Энергия, необходимая для разрушения металла при динамической нагрузке, в этом случае увеличивается, ударная вязкость возрастает.
Увеличение концентрации углерода у белых чугунов повышает их твердость от HRC 35 при 2,2 % С до HRC 48 при 4,3 % С и соответственно хрупкость. Динамическая прочность белых чугунов близка к нулю. С увеличением углерода в серых чугунах увеличивается количество и размер графитных включений, что также снижает прочность.
Углерод оказывает влияние и на свойства серых чугунов. Увеличение содержания углерода ведет к увеличению количества графитовых включению и снижению механических свойств, но значительно улучшают литейные свойства.
Также значительно влияние размеров и формы графитных включений на механические свойства у серых чугунов (рис. 4.4.3). Измельчая графитные включения, повышают в 2−3 раза предел прочности чугуна. У чугунов, имеющих крупные, пересекающиеся графитные включения, предел прочности при растяжении уменьшается до 120 МПа. Наиболее высокую прочность имеют высокопрочные чугуны с шаровидным графитом. Наибольшее относительное удлинение при достаточно высокой прочности (370 МПа) имеют ковкие ферритные чугуны (δ до 12 %).
Рис. 4.4.3. Зависимость механических свойств чугуна от формы и размеров графитовых включений (СЧ 12 – с грубопластинчатым графитом, СЧ 32 – с мелким завихрённым графитом)
Источник
Влияние углерода и примесей на свойства сталей.
Углеродистые стали являются основными. Их свойства определяются количеством углерода и содержанием примесей, которые взаимодействуют с железом и углеродом.
Влияние углерода.
Влияние углерода на свойства сталей показано на рис. 10.1
Рис.10.1. Влияние углерода на свойства сталей
С ростом содержания углерода в структуре стали увеличивается количество цементита, при одновременном снижении доли феррита. Изменение соотношения между составляющими приводит к уменьшению пластичности, а также к повышению прочности и твердости. Прочность повышается до содержания углерода около 1%, а затем она уменьшается, так как образуется грубая сетка цементита вторичного.
Углерод влияет на вязкие свойства. Увеличение содержания углерода повышает порог хладоломкости и снижает ударную вязкость.
Повышаются электросопротивление и коэрцитивная сила, снижаются магнитная проницаемость и плотность магнитной индукции.
Углерод оказывает влияние и на технологические свойства. Повышение содержания углерода ухудшает литейные свойства стали (используются стали с содержанием углерода до 0,4 %), обрабатываемость давлением и резанием, свариваемость. Следует учитывать, что стали с низким содержанием углерода также плохо обрабатываются резанием.
Влияние примесей.
В сталях всегда присутствуют примеси, которые делятся на четыре группы. 1.Постоянные примеси: кремний, марганец, сера, фосфор.
Марганец и кремний вводятся в процессе выплавки стали для раскисления, они являются технологическими примесями.
Содержание кремния не превышает 0,35…0,4 %. Кремний, дегазируя металл, повышает плотность слитка.
Содержание фосфора в стали 0,025…0,045 %. Фосфор, увеличивает предел прочности и предел текучести , но снижает пластичность и вязкость.
Располагаясь вблизи зерен, увеличивает температуру перехода в хрупкое состояние, вызывает хладоломкость, уменьшает работу распространения трещин, Повышение содержания фосфора на каждую 0,01 % повышает порог хладоломкости на 20…25oС.
Содержание серы в сталях составляет 0,025…0,06 %. Сера – вредная примесь, попадает в сталь из чугуна. При взаимодействии с железом образует химическое соединение – сульфид серы FeS, которое, в свою очередь, образует с железом легкоплавкую эвтектику с температурой плавления 988oС. При нагреве под прокатку или ковку эвтектика плавится, нарушаются связи между зернами. При деформации в местах расположения эвтектики возникают надрывы и трещины, заготовка разрушается – явление красноломкости.
Красноломкость – повышение хрупкости при высоких температурах
Сера снижает механические свойства, особенно ударную вязкость а и пластичность ( и ), а так же предел выносливости. Она ухудшают свариваемость и коррозионную стойкость.
2. Скрытые примеси – газы (азот, кислород, водород) – попадают в сталь при выплавке.
3. Специальные примеси – специально вводятся в сталь для получения заданных свойств. Примеси называются легирующими элементами, а стали – легированные сталями.
Структурное фазовое превращение при термообработки сталей. Образование аустенитав доэвтектоидных и заэвтектоидных сталей , величина зерна, наследственная зернистость.
Фазовая перекристаллизация, включающая полиморфное или эвтектоидное превращение, приводит к коренной перестройке структуры по всему объему сплава. Полиморфное превращение в металлах можно использовать для устранения текстуры и изменения размера зерна. Эвтектоидное превращение в цветных сплавах пока редко используют как основу отжига 2-го рода.
Фазовые превращения, которые совершаются в стали также, как и превращения при кристаллизации обуславливается тем, вследствие изменения внешних факторов (температуры) происходит переход из одного состояния в другое, оказавшееся более устойчивым при данной температуре. Основными в стали являются три структуры – аустенит, мартенсит, перлит. Основные превращения в стали характеризуются переходом этих структур из одного в другую.
При термической обработке стали наблюдаются 4 основных превращения..
1. Превращение перлита в аустенит, протекающее выше точки А1, т. е. выше температуры стабильного равновесия А«П . При этих температурах их 3-х основных структур минимальной свободной энергией обладает аустенит.
Fea (С) + Fe2С ® Fe g(С)
2. Превращение аустенита в перлит, протекающее ниже Ас1
Feg (С) ® Fea + Fe2(С)
3. Превращение аустенита в мартенсит
Feg (С) ® Fea(C)
4. Превращение мартенсита в феррито-карбидную смесь
Fea(С) ® Fea + Fe2С
Образование аустенита .
1. Превращение перлита в аустенит в полном соответствии с диаграммой Fе-С может совершится лишь при очень медленном нагреве. Чем выше температура, тем больше скорость превращения.
2. Рост аустенитного зерна. На первой стадии превращения перлита в аустенит происходит образование большого количества мелких зерен аустенита. Размеры этих зерен характеризует так называемое начальное зерно аустенита.
Дальнейший нагрев или выдержка обуславливает рост аустенитных зерен. Этот процесс протекает самопроизвольно т.к. идет с уменьшением поверхностной энергии за счет уменьшения суммарной поверхности зерен. Высокая температура лишь обеспечивает достаточную скорость протекания процесса. Различают 2 типа сталей– наследственно мелкозернистые и наследственно крупнозернистые.
1-й характеризуется малой склонностью к росту зерна, 2-й – повышенной склонностью.
В наследственно мелкозернистой (а) стали при переходе через АI сопровождается уменьшением величины зерна. Это зерно не растет при дальнейшем нагреве до 950-1000°С
Рост начинается выше 1000° С. У крупнозернистой стали рост зерен начинается при переходе через критическую точку (б). Таким образом, под наследственной зернистостьюнужно понимать склонность аустенитного зерна к росту.
Размер зерна, наблюдаемый в стали после термической обработки называется действенным. Следовательно, различают 3 характеристики размера зерна стали :
1. Начальное зерно – размер зерна аустенита в момент окончания
превращения П « А
2. Наследственное зерно, определяющее склонность зерна аустенита к
росту.
3. Действительное зерно – размер зерна аустенита в данных конкретных условиях.
Влияние углерода и примесей на свойства сталей.
Углеродистые стали являются основными. Их свойства определяются количеством углерода и содержанием примесей, которые взаимодействуют с железом и углеродом.
Влияние углерода.
Влияние углерода на свойства сталей показано на рис. 10.1
Рис.10.1. Влияние углерода на свойства сталей
С ростом содержания углерода в структуре стали увеличивается количество цементита, при одновременном снижении доли феррита. Изменение соотношения между составляющими приводит к уменьшению пластичности, а также к повышению прочности и твердости. Прочность повышается до содержания углерода около 1%, а затем она уменьшается, так как образуется грубая сетка цементита вторичного.
Углерод влияет на вязкие свойства. Увеличение содержания углерода повышает порог хладоломкости и снижает ударную вязкость.
Повышаются электросопротивление и коэрцитивная сила, снижаются магнитная проницаемость и плотность магнитной индукции.
Углерод оказывает влияние и на технологические свойства. Повышение содержания углерода ухудшает литейные свойства стали (используются стали с содержанием углерода до 0,4 %), обрабатываемость давлением и резанием, свариваемость. Следует учитывать, что стали с низким содержанием углерода также плохо обрабатываются резанием.
Влияние примесей.
В сталях всегда присутствуют примеси, которые делятся на четыре группы. 1.Постоянные примеси: кремний, марганец, сера, фосфор.
Марганец и кремний вводятся в процессе выплавки стали для раскисления, они являются технологическими примесями.
Содержание кремния не превышает 0,35…0,4 %. Кремний, дегазируя металл, повышает плотность слитка.
Содержание фосфора в стали 0,025…0,045 %. Фосфор, увеличивает предел прочности и предел текучести , но снижает пластичность и вязкость.
Располагаясь вблизи зерен, увеличивает температуру перехода в хрупкое состояние, вызывает хладоломкость, уменьшает работу распространения трещин, Повышение содержания фосфора на каждую 0,01 % повышает порог хладоломкости на 20…25oС.
Содержание серы в сталях составляет 0,025…0,06 %. Сера – вредная примесь, попадает в сталь из чугуна. При взаимодействии с железом образует химическое соединение – сульфид серы FeS, которое, в свою очередь, образует с железом легкоплавкую эвтектику с температурой плавления 988oС. При нагреве под прокатку или ковку эвтектика плавится, нарушаются связи между зернами. При деформации в местах расположения эвтектики возникают надрывы и трещины, заготовка разрушается – явление красноломкости.
Красноломкость – повышение хрупкости при высоких температурах
Сера снижает механические свойства, особенно ударную вязкость а и пластичность ( и ), а так же предел выносливости. Она ухудшают свариваемость и коррозионную стойкость.
2. Скрытые примеси – газы (азот, кислород, водород) – попадают в сталь при выплавке.
3. Специальные примеси – специально вводятся в сталь для получения заданных свойств. Примеси называются легирующими элементами, а стали – легированные сталями.
Источник
Содержание углерода и легирующих элементов определяет свойства углеродистых сталей. Состав сплава содержит железо, углерод, магний, кремний, марганец, серу и фосфор. Количество одного компонента по отношению к общей массе определяет вязкость, пластичность, прочность и твердость металла. Углеродистые стали классифицируют по химическому составу, способу изготовления, назначению и степени раскисления. Металлопрокат производят из разных марок стали. Компания «Стальмет» продает металлопродукцию из углеродистых сталей, соответствующих ГОСТу 380-2005 и 1050-2005.
Состав стали с углеродом
Технология производства не полностью удаляет примеси из стали. Они занимают малую процентную долю, но присутствуют во всех углеродистых сталях. Содержание углерода разделяет сталь на углеродистую и легированную. Углерод добавляют намеренно, чтобы изменить технические характеристики и механические свойства сталей. Наличие примесей зависит от выбранной плавки сталей. Процентное содержание разных элементов в составе стали:
- железо — до 99 %;
- углерод — до 2,14 %;
- кремний — до 1 %;
- марганец — до 1 %;
- фосфор — до 0,6 %;
- сера — до 0,5 %.
Сталь содержит незначительное количество водорода, кислорода и азота.
Какие свойства у стали с разным содержанием углерода?
Механические свойства стали зависят от количества углерода. Увеличение или снижение содержания углерода, даже в сотых долях процента, предопределяет сферу применения металла. Структура углеродистой стали меняется от содержания цементита и феррита. Когда в сталь добавляют больше углерода, сплав становится твердым, прочным и упругим. Когда уменьшают, улучшают ее пластичность и сопротивление удару.
В зависимости от того, сколько углерода в составе сплава, различают несколько видов стали:
- Низкоуглеродистые содержат меньше 0,25 % углерода. Пластичные, но легко деформируемые. Обрабатываются в холодном состоянии и под действием высокой температуры.
- Среднеуглеродистые — 0,3-0,6 %. Пластичные, текучие и среднепрочные. Из них изготавливают детали и конструкции, которые будут использовать в нормальных условиях.
- Высокоуглеродистые — 0,6-2 %. Износостойкие, прочные и дорогие углеродистые стали с низкой вязкостью. Плохо поддаются сварке без предварительного разогрева обрабатываемой зоны до +225оС.
Низкоуглеродистые и среднеуглеродистые стали обрабатывать и варить проще, чем высокоуглеродистые.
Виды углеродистой стали по степени раскисления
У углеродистой стали разная степень раскисления. Бывают спокойные, кипящие и полуспокойные сплавы. Названия связаны с содержанием вредных примесей — оксидом железа. Чем меньше кислорода в сплаве, тем стабильнее и долговечнее стали. После разливки сталь выделяет газы и затвердевает.
В спокойных сталях кислород удален почти полностью, поэтому у них однородная структура и равномерное распределение состава. Полуспокойные чаще содержат 0,15-0,3 % углерода. Таким сталям свойственна неравномерная структура из-за частичного раскисления сплава. Больше всего кислорода у кипящих сталей. Такое раскисление приводит к разному химическому составу. В кипящих сталях много примесей: углерода, азота, серы и фосфора.
Чем отличаются инструментальные и конструкционные стали?
Сфера применения и способ изготовления — главные отличия сталей. Конструкционные углеродистые стали выплавляют в конвертерах и мартеновских печах. Они бывают высокого и обыкновенного качества. Их разделяют на группы А, Б и В. Маркируют соответственно буквами и цифрами. В обозначении буква говорит о группе стали, а цифры указывают на содержание углерода, увеличенное в 100 раз. Чем больше значение, тем прочнее сталь. Стали обыкновенного качества с повышенным содержанием марганца маркируются буквой «Г».
Сталь группы А поставляют по механическим свойствам, группы Б — по химическому составу, группы В — по механическим свойствам и химическому составу. Это означает, что сталь группы А обладает заявленными свойствами, а сталь группы Б отвечает нормативной документации.
Углеродистую инструментальную сталь выплавляют в мартеновской или электрической печи. Она бывает спокойной, полуспокойной и кипящей. Ее разделяют на качественную и высококачественную сталь. Доля примесей в качественной инструментальной стали регламентирована: серы должно быть не более 0,4 %, фосфора — не больше 0,6 %. Цифра в маркировке говорит о содержании углерода в сотых долях. Также она обозначает условный номер марки материала.
Сферы применения углеродистых сталей
Углеродистые стали обыкновенного качества используют для изготовления двутавра, уголка, швеллера, прута, листа и другого проката. В производстве инструментов и деталей для разных областей машиностроения применяют углеродистую сталь высокого качества.
Источник
По мере повышения концентрации углерода в стали и чугуне изменяются структура и их механические свойства. Прочность горячекатаной стали в нормализованном состоянии с увеличением содержания углерода повышается, а пластичность снижается (рис. 4.4.2). Повышение прочности достигает предельного значения при содержании углерода около 0,9 %. При дальнейшем увеличении количества углерода наблюдается возрастание твердости, но снижение прочности. Это объясняется влиянием хрупкой цементитной сетки, которая окружает зерна перлита и уменьшает прочность связи между ними.
Кроме того, с увеличением содержания углерода снижаются технологические свойства стали, увеличивается усадка, ухудшается жидкотекучесть, ковкость и свариваемость, затрудняется механическая обработка. Поэтому для сварных конструкций используют стали с пониженным содержанием углерода (до 0,3 %), а штамповки изготовляют из стали с содержанием углерода до 0,5 %.
Рис. 4.4.2. Зависимость механических свойств стали от содержания углерода
Следует остановиться на влиянии формы цементита на механические свойства перлита. Частички цементита в перлите могут быть не только в виде пластинок, но и в виде округлых зерен.
Изменение формы цементита существенно изменяет механические свойства стали и прежде всего пластичность. У стали со структурой зернистого перлита предел прочности и твердости ниже на 15−20 %, чем у стали со структурой пластинчатого перлита, а относительное удлинение выше в 2−4 раза. Например, сталь с содержанием 0,8 % С со структурой пластинчатого перлита имеет предел прочности σВ = 800 МПа, относительное удлинение δ = 14 %, а со структурой зернистого перлита σВ = 590 МПа,
δ =29 %. Повышенная пластичность зернистого перлита объясняется тем, что глобулярные частицы цементита оказывают меньшее сопротивление развитию пластической деформации по сравнению с пластинчатыми. Энергия, необходимая для разрушения металла при динамической нагрузке, в этом случае увеличивается, ударная вязкость возрастает.
Увеличение концентрации углерода у белых чугунов повышает их твердость от HRC 35 при 2,2 % С до HRC 48 при 4,3 % С и соответственно хрупкость. Динамическая прочность белых чугунов близка к нулю. С увеличением углерода в серых чугунах увеличивается количество и размер графитных включений, что также снижает прочность.
Углерод оказывает влияние и на свойства серых чугунов. Увеличение содержания углерода ведет к увеличению количества графитовых включению и снижению механических свойств, но значительно улучшают литейные свойства.
Также значительно влияние размеров и формы графитных включений на механические свойства у серых чугунов (рис. 4.4.3). Измельчая графитные включения, повышают в 2−3 раза предел прочности чугуна. У чугунов, имеющих крупные, пересекающиеся графитные включения, предел прочности при растяжении уменьшается до 120 МПа. Наиболее высокую прочность имеют высокопрочные чугуны с шаровидным графитом. Наибольшее относительное удлинение при достаточно высокой прочности (370 МПа) имеют ковкие ферритные чугуны (δ до 12 %).
Рис. 4.4.3. Зависимость механических свойств чугуна от формы и размеров графитовых включений (СЧ 12 – с грубопластинчатым графитом, СЧ 32 – с мелким завихрённым графитом)
Источник