От каких факторов зависят свойства отпущенной углеродистой стали
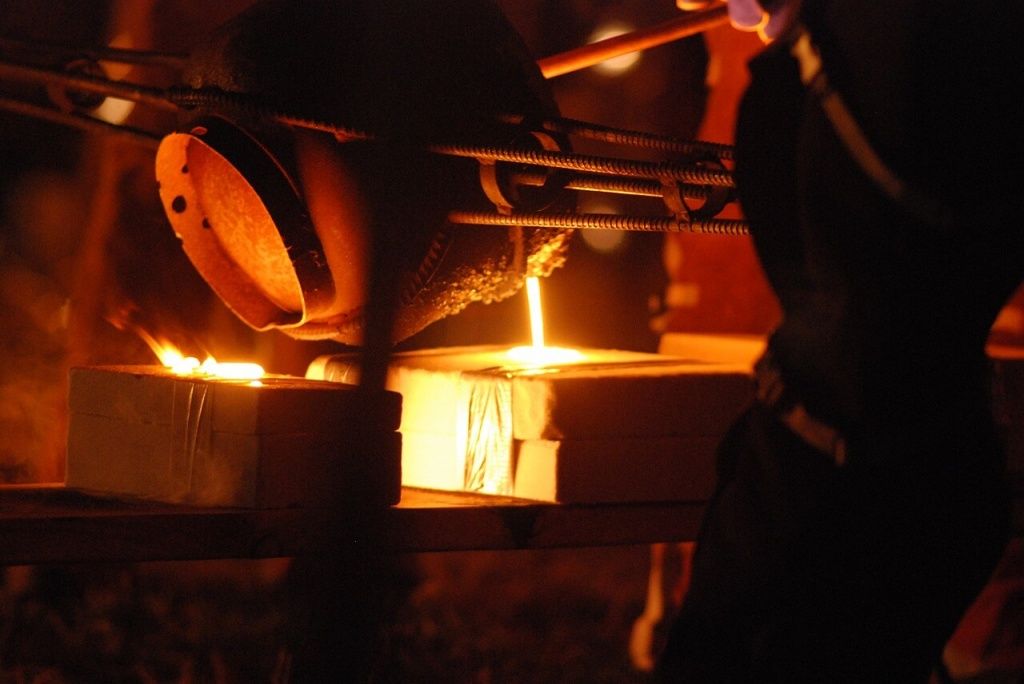
Свойства углеродистых сталей зависят от содержания углерода, а также от содержания постоянных и скрытых примесей При одинаковом содержании углерода кипящие, полуспокойные и спокойные стали имеют близкие величины прочностных свойств и различаются значениями характеристик пластичности. Содержание кремния в спокойной стали составляет 0,15-0,35%, в полуспокойной – 0,05-0,15%, в кипящей – до 0,05%.
Влияние содержания углерода на механические свойства сталей.
7.2. 1. Как зависят свойства углеродистых сталей от содержания углерода?
Углерод является важнейшим элементом, определяющим структуру и свойства углеродистой стали. Даже малое изменение содержания углерода оказывает заметное влияние на свойства сталей. С увеличением углерода в структуре стали растет содержание цементита.. При содержании до 0,8% С сталь состоит из феррита и перлита, при содержании более 0,8%С в структуре стали кроме перлита появляется структурно свободный цементит. Феррит имеет низкую прочность, но сравнительно пластичен. Цементит характеризуется высокой твердостью, но хрупок. Поэтому с ростом содержания углерода увеличивается твердость и прочность и уменьшается вязкость и пластичность стали (рис.1).
Рис. 1. Зависимость механических свойств стали от содержания углерода.
Рост прочности происходит при содержании в стали до 0,8-1,0% С.
7.2. 2. Чем обусловлен рост прочности до 0,8 –1,0%С?
При содержании до 0,8% С сталь состоит из феррита и перлита, при содержании более 0,8%С в структуре стали кроме перлита появляется структурно свободный цементит. Феррит имеет низкую прочность, но сравнительно пластичен. Цементит характеризуется высокой твердостью, но хрупок. Поэтому с ростом содержания углерода увеличивается твердость и прочность и уменьшается вязкость и пластичность
7.2. 3. Почему при увеличении содержания углерода более 1,0% С уменьшается не только пластичность, но и прочность стали? Это связано с образованием сетки хрупкого цементита вокруг перлитных зерен, легко разрушающейся при нагружении.
Какое влияние оказывает углерод на технологические свойства?
Углерод оказывает существенное влияние на свариваемость, обрабатываемость давлением и резанием. С увеличением содержания углерода ухудшается свариваемость, а также способность деформироваться в горячем и особенно в холодном состоянии. Лучше всего обрабатывается резанием среднеуглеродистые стали, содержащие 0,3-0,4%С. Низкоуглеродистые стали при механической обработке дают плохую поверхность и трудноудаляемую стружку. Высокоуглеродистые стали имеют повышенную твердость, что снижает стойкость инструмента.
7.3. Влияние примесей на свойства стали
7.3.1. Назовите постоянные и скрытые примеси в углеродистых сталях?
Постоянными примесями в углеродных сталях являются марганец, кремний, сера, фосфор, а скрытые примеси – газы: кислород, азот, водород.
Охарактеризуйте влияние марганца
Полезными примесями являются марганец и кремний. Их вводят в сталь в процессе выплавки для раскисления:
Fe+Mn → MnO+Fe; 2FeO+Si → SiO2+2Fe/
В углеродистой стали содержится до 0,8% Mn. Марганец, помимо раскисления, в этих количествах полностью растворяется в феррите и упрочняет его, увеличивает прокаливаемость стали, а также уменьшает вредное влияние серы, связывая еетугоплавкие сульфиды:
FeSв +Mn → MnS+Fe.
7.3.3. Охарактеризуйте влияние кремния?
В полностью раскисленной углеродистой стали содержится до 0,4%Si. Кремний является полезной примесью, так как эффективно раскисляет сталь и, полностью растворяясь в феррите, способствует его упрочнению.
7.3.4. Охарактеризуйте влияние серы?
Сера является вредной примесью. Основной источник серы в стали – исходное сырье (чугун). Сера снижает пластичность и вязкость стали, а также сообщает стали красноломкость при прокатке и ковке. Сера нерастворима в стали. Она образует с железом соединение FeS – сульфид железа, хорошо растворимый в металле. При малом содержании марганца благодаря высокой ликвации серы в стали может образоваться легкоплавкая эвтектика Fe-FeS
(tпл =988 ºC). Эвтектика располагается по границам зерен. При нагреве стальных заготовок до температуры горячей деформации включения эвтектики сообщают стали хрупкость, а при некоторых условиях могут даже плавиться и при деформировании образовывать надрывы и трещины. Поэтому содержание серы в стали должно быть как можно меньше.
Повышенное (до 0,2%) содержание серы допускается лишь в автоматных сталях для изготовления крепежных деталей неответственного назначения, так как сера улучшает обрабатываемость стали.
7.3.5. Какой элемент вводят для устранения вредного влияния серы?
Марганец устраняет красноломкость, так как сульфиды марганца не образуют сетки по границам зерен и имеют температуру плавления около 1620 ºC, что выше температуры горячей деформации. Вместе с тем сульфиды марганца, как и другие неметаллические включения, также снижают вязкость и пластичность, уменьшают усталостную прочность стали.
7.3.6. Охарактеризуйте влияние фосфора?
Основной источник фосфора – руды, из которых выплавляется исходный чугун. Фосфор является вредной примесью. Растворяясь в феррите до 1,2%, фосфор уменьшает его пластичность. Фосфор резко отличается от железа по типу кристаллической решетки, диаметру атомов и их строению. Поэтому фосфор располагается вблизи границ зерен и способствует их охрупчиванию, повышая температурный порог хладноломкости.
7.3.7. Охарактеризуйте влияние скрытых примесей.
Скрытые примеси – кислород, азот, водород – присутствуют в стали либо в виде твердого раствора в феррите, либо в составе химических соединений (нитриды, оксиды), либо в свободном состоянии в порах металла. Кислород и азот мало растворимы в феррите. Они загрязняют сталь хрупкими неметаллическими включениями, что снижает вязкость и пластичность стали. Водород находится в твердом растворе и особенно сильно охрупчивает сталь. Повышенное содержание водорода, особенно в хромистых и хромоникелевых сталях, приводит к образованию внутренних трещин – флокенов.
Даже небольшие концентрации газов оказывают резко отрицательное влияние на свойства, ухудшая пластические и вязкие характеристики стали. Поэтому вакуумирование является важной операцией для улучшения свойств стали. Кроме того, в углеродистых сталях присутствуют такие случайные примеси, как Cr, Ni, Cu, наличие которых обусловлено загрязненностью шихты.
Источник
Углеродистые стали. Закаленная углеродистая сталь характеризуется не только высокой твердостью, но и очень большой склонностью к хрупкому разрушению. Кроме того, при закалке возникают значительные остаточные напряжения. Поэтому закалку углеродистых сталей обычно не применяют как окончательную операцию. Для увеличения вязкости и уменьшения закалочных напряжений после закалки применяют отпуск.
На рис. 3.5 видно, что до температуры отпуска около 100 °С твердость закаленной стали или практически не меняется, или слабо (на 1—2 НЛО) возрастает. С дальнейшим повышением температуры отпуска твердость плавно снижается.
С ростом температуры отпуска разупрочнение усиливается из-за следующих причин: 1) уменьшения концентрации углерода в а-растворе; 2) нарушения когерентности на границе карбид — матрица и снятия упругих микронапряжений; 3) коагуляции карбидов и увеличения межчастичного расстояния; 4) развития возврата и рекристаллизации. В разных температурных интервалах преобладает действие разных факторов разупрочнения в соответствии с интенсивностью развития тех или иных структурных изменений.
В высокоуглеродистых сталях, содержащих значительное количество остаточного аустенита, распад его с выделением карбида задерживает падение твердости, а в интервале температур 200—250 °С даже несколько увеличивает ее.
Прочностные характеристики углеродистой стали (временное сопротивление, предел текучести и твердость) непрерывно уменьшаются с ростом температуры отпуска выше 300 °С, а показатели пластичности (относительное удлинение и сужение) непрерывно повышаются (рис. 3.6). Ударная вязкость начинает интенсивно возрастать при отпуске выше 300 °С. Максимальной ударной вязкостью обладает сталь с сорбитной структурой, отпущенная при 600 °С. Некоторое снижение ударной вязкости при температурах отпуска выше 600 °С можно объяснить тем, что частицы цементита по границам ферритных зерен, растущие вследствие растворения частиц внутри а-фазы, становятся слишком грубыми.
В соответствии с температурой нагрева различают низкий, средний и высокий отпуск.
Низкий отпуск на отпущенный мартенсит (120—250 °С) широко применяют после закалки инструментов, цементованных и циани-рованных изделий и после поверхностной закалки. Цель низкого отпуска — уменьшение остаточных закалочных напряжений. Температуру низкого отпуска выбирают такой, чтобы твердость и износостойкость не снизились или слабо снизились. Выдержка при температуре низкого отпуска обычно не превышает 1—3 ч; с дальнейшим увеличением выдержки остаточные напряжения очень слабо уменьшаются.
Разновидность низкого отпуска — стабилизирующий отпуск. В закаленной стали даже при комнатной температуре, а тем более в результате климатических колебаний температуры происходят медленные (в течение многих лет) процессы распада мартенсита, перехода остаточного аустенита в мартенсит и снятия напряжений. Все эти явления ведут к постепенному изменению размеров изделия. Для таких изделий, как мерительный инструмент высокого класса точности и прецизионные подшипники, недопустимы изменения размеров даже на насколько микронов. Стабилизации мартенсита и напряженного состояния достигают низким (стабилизирующим) отпуском при 100—180 °С с выдержкой до 30, а иногда и до 150 ч.
няс
- 60
- 40
- 30
- 50
- 100
- 200 400 г. *С
Рис. 3.5. Зависимость твердости углеродистых сталей разного состава от температуры отпуска
Й
О’_I_I_I_
300 400 500 600 г. #С
Рис. 3.6. Влияние температуры отпуска на механические свойства стали
Средний отпуск на троостит (350—450 °С) используют тогда, когда необходимо получить в стали сочетание высокой прочности, упругости и, вместе с тем, достаточной вязкости. Среднему отпуску подвергают пружины и рессоры.
Высокий отпуск на сорбит (450—650 °С) широко применяют в машиностроении к изделиям из конструкционной стали, которые должны характеризоваться не только достаточной прочностью, но и хорошей сопротивляемостью ударным нагрузкам. Выдержку при высоком отпуске (обычно несколько часов) подбирают опытным путем для получения заданного комплекса свойств.
Двойная операция получения сорбита — закалка с высоким отпуском — называется улучшением. Эту операцию применяют к среднеуглеродистым сталям, содержащим от 0,35 до 0,6% С. Такие стали называют улучшаемыми в отличие от малоуглеродистых цементуемых.
Скорость охлаждения с температуры отпуска не влияет на механические свойства углеродистых сталей, и если не опасны термические напряжения, то можно проводить ускоренное охлаждение.
Легированные стали. Легирующие элементы, затрудняющие распад мартенсита и коагуляцию карбидов, смещают температурную границу начала интенсивного разупрочнения при отпуске с 200—300 до 450—550 °С. Повышение красностойкости закаленной стали, т.е. способности ее сопротивляться смягчению при нагреве, — одна
из основных целей легирования в производстве инструмента.
Для конструкционных легированных сталей весьма важно, что специальные карбиды выделяются при высоком отпуске в более дис-
персной форме, чем цементит. Это обеспечивает повышенную вязкость, так как микропустоты (очаги разрушения) зарождаются около мелких частиц специального карбида труднее, чем около более крупных частиц цементита.
Отпускная хрупкость. Отпускная хрупкость присуща многим сталям. В результате медленного охлаждения с температуры высокого отпуска ударная вязкость легированной стали может оказаться в несколько раз (и даже на порядок) меньше, чем после охлаждения в воде с той же температуры. Есть два температурных интервала, при которых у конструкционных сталей ударная вязкость заметно снижается: 250—350 и 500—600 °С. Понижение вязкости соответственно называют отпускной хрупкостью I и II рода.
Понижение ударной вязкости после отпуска при 250—350 °С наблюдается у всех конструкционных сталей независимо от степени легирования. Заметное падение ударной вязкости после отпуска 500—600 °С наблюдается только у легированных конструкционных сталей — хромистых, марганцевых, хромоникелевых, хромомарганцевых и т.д. Снижение вязкости почти не происходит в случае быстрого охлаждения от температуры отпуска (в воде или масле). Отпускная хрупкость II рода заметно подавляется даже при медленном охлаждении от температуры отпуска дополнительным легированием сталей молибденом или вольфрамом в количестве 0,3 и 1% соответственно.
Источник
Описанные выше изменения структуры сталей при отпуске приводят к значительному изменению их механических свойств.
Общей тенденцией изменения свойств в стали при отпуске является снижение ее прочностных характеристик (твердости НВ, К2, о«) и повышение пластических (8, I//). Причем во всех трех интервалах отпуска суммарное изменение механических свойств обусловлено рядом структурных факторов, действующих часто в противоположных направлениях. Например, снижение тетратональности мартенсита приводит к снижению прочностных характеристик и увеличению пластических. Однако происходящее при этом выделение мелкодисперсных карбидов, особенно некогерентно связанных с мартенситными кристаллами или образование вместо однофазного остаточного аустенита, областей с гетерогенной феррито-карбидной – в углеродистых сталях, или марген- ситно-карбидной в легированных сталях, повышает прочностные и снижает пластические характеристики. Конечный результат зависит от соотношения вкладов действующих факторов. Причиной различий действия указанных структур на свойства является различие в сопротивлении движению дислокаций.
Так, в однофазных областях остаточного аустенита и слабо искаженных кристаллах мартенсита отпуска (с меньшей теграго- нальностью) дислокации движутся легче, их пробег от одного препятствия до другого – больше. А известно, что именно средняя длина пробега дислокаций определяет пластические характеристики (чем она больше, тем выше пластичность). Выделение когерентно связанных с мартенситом мелкодисперсных частиц карбидов значительного повышения сопротивления движению дислокаций не оказывает, и дислокации могут перерезать указанные пластинки.
Когда же размеры карбидов увеличиваются, они становятся некогерентными и движение дислокаций у карбидов тормозится. Для дальнейшего их движения требуется приложить большие напряжения; прочностные характеристики сталей с такой структурой увеличиваются.
Зависимость механических свойств стали с 0,7 % С от температуры отпуска приведена на рис. 80.
Рис. 80. Влияние температуры отпуска на механические свойства стали У7
Как видно из рис. 80, твердость НВ, ав монотонно снижаются с ростом температуры, а S и ^/монотонно растут.
В сталях с высоким содержанием углерода в интервале температур второго превращения при отпуске твердость зависит от количества остаточного аустенита и снижается медленнее с ростом температуры. В легированных сталях, содержащих значительное количество карбидообразующих элементов, при температурах 500 – 550 °С твердость не только не снижается, но даже растет, что обусловлено выделением специальных карбидов.
В сталях различают низкий отпуск (с нагревом до 250 °С), средний (350 – 500 °С) и высокий (500 – 650 °С). Каждый из этих видов отпуска, создавая описанные выше сгруктуры, устраняет частично или полностью остаточные напряжения, возникшие при закалке. Для полного снятия напряжений рекомендуется применять высокий отпуск.
Пластические характеристики легированных сталей S, ц/ с повышением температуры отпуска растут. Ударная же вязкость (КС), с ростом температуры отпуска изменяется немонотонно.
При низких температурах отпуска (200 – 250 °С) ударная вязкость растет (для закаленных сталей она низкая).
Для всех легированных конструкционных сталей имеется два температурных интервала, в которых с ростом температуры отпуска ударная вязкость не растет, а падает. Первый интервал соответствует температурам 250 – 350 °С, а второй – температурам 500 – 550 °С. Явление снижения ударной вязкости при отпуске получило название отпускной хрупкости.
Различают два вида отпускной хрупкости:
- 1. Отпускная хрупкость I рода (необратимая) – наблюдается при температурах 250 – 350 °С и повторным нагревом не устраняется. Для ее устранения требуется нагрев до температур выше 400 °С, что снижает прочностные характеристики. Хрупкость при отпуске в интервале температур 250 – 350 °С связана с неоднородным по объему распадом мартенсита.
- 2. Обратимая отпускная хрупкость II рода – наблюдается при отпуске легированных сталей и при их длительном пребывании в интервале температур 500 – 550 °С. Если охлаждение после отпуска проводить быстро, то отпускная хрупкость не появляется.
Наиболее вероятной причиной появления обратимой отпускной хрупкости является образование карбидов но границам зерен и адсорбция на границах зерен фосфора, серы и других элементов, приводящая к более легкому зарождению трещин.
Обратимая отпускная хрупкость может быть устранена повторным нагревом до 600 – 650 °С и быстрым охлаждением.
Термическую обработку, заключающуюся в закалке и последующем высоком отпуске, называют улучшением.
Источник
Содержание углерода и легирующих элементов определяет свойства углеродистых сталей. Состав сплава содержит железо, углерод, магний, кремний, марганец, серу и фосфор. Количество одного компонента по отношению к общей массе определяет вязкость, пластичность, прочность и твердость металла. Углеродистые стали классифицируют по химическому составу, способу изготовления, назначению и степени раскисления. Металлопрокат производят из разных марок стали. Компания «Стальмет» продает металлопродукцию из углеродистых сталей, соответствующих ГОСТу 380-2005 и 1050-2005.
Состав стали с углеродом
Технология производства не полностью удаляет примеси из стали. Они занимают малую процентную долю, но присутствуют во всех углеродистых сталях. Содержание углерода разделяет сталь на углеродистую и легированную. Углерод добавляют намеренно, чтобы изменить технические характеристики и механические свойства сталей. Наличие примесей зависит от выбранной плавки сталей. Процентное содержание разных элементов в составе стали:
- железо — до 99 %;
- углерод — до 2,14 %;
- кремний — до 1 %;
- марганец — до 1 %;
- фосфор — до 0,6 %;
- сера — до 0,5 %.
Сталь содержит незначительное количество водорода, кислорода и азота.
Какие свойства у стали с разным содержанием углерода?
Механические свойства стали зависят от количества углерода. Увеличение или снижение содержания углерода, даже в сотых долях процента, предопределяет сферу применения металла. Структура углеродистой стали меняется от содержания цементита и феррита. Когда в сталь добавляют больше углерода, сплав становится твердым, прочным и упругим. Когда уменьшают, улучшают ее пластичность и сопротивление удару.
В зависимости от того, сколько углерода в составе сплава, различают несколько видов стали:
- Низкоуглеродистые содержат меньше 0,25 % углерода. Пластичные, но легко деформируемые. Обрабатываются в холодном состоянии и под действием высокой температуры.
- Среднеуглеродистые — 0,3-0,6 %. Пластичные, текучие и среднепрочные. Из них изготавливают детали и конструкции, которые будут использовать в нормальных условиях.
- Высокоуглеродистые — 0,6-2 %. Износостойкие, прочные и дорогие углеродистые стали с низкой вязкостью. Плохо поддаются сварке без предварительного разогрева обрабатываемой зоны до +225оС.
Низкоуглеродистые и среднеуглеродистые стали обрабатывать и варить проще, чем высокоуглеродистые.
Виды углеродистой стали по степени раскисления
У углеродистой стали разная степень раскисления. Бывают спокойные, кипящие и полуспокойные сплавы. Названия связаны с содержанием вредных примесей — оксидом железа. Чем меньше кислорода в сплаве, тем стабильнее и долговечнее стали. После разливки сталь выделяет газы и затвердевает.
В спокойных сталях кислород удален почти полностью, поэтому у них однородная структура и равномерное распределение состава. Полуспокойные чаще содержат 0,15-0,3 % углерода. Таким сталям свойственна неравномерная структура из-за частичного раскисления сплава. Больше всего кислорода у кипящих сталей. Такое раскисление приводит к разному химическому составу. В кипящих сталях много примесей: углерода, азота, серы и фосфора.
Чем отличаются инструментальные и конструкционные стали?
Сфера применения и способ изготовления — главные отличия сталей. Конструкционные углеродистые стали выплавляют в конвертерах и мартеновских печах. Они бывают высокого и обыкновенного качества. Их разделяют на группы А, Б и В. Маркируют соответственно буквами и цифрами. В обозначении буква говорит о группе стали, а цифры указывают на содержание углерода, увеличенное в 100 раз. Чем больше значение, тем прочнее сталь. Стали обыкновенного качества с повышенным содержанием марганца маркируются буквой «Г».
Сталь группы А поставляют по механическим свойствам, группы Б — по химическому составу, группы В — по механическим свойствам и химическому составу. Это означает, что сталь группы А обладает заявленными свойствами, а сталь группы Б отвечает нормативной документации.
Углеродистую инструментальную сталь выплавляют в мартеновской или электрической печи. Она бывает спокойной, полуспокойной и кипящей. Ее разделяют на качественную и высококачественную сталь. Доля примесей в качественной инструментальной стали регламентирована: серы должно быть не более 0,4 %, фосфора — не больше 0,6 %. Цифра в маркировке говорит о содержании углерода в сотых долях. Также она обозначает условный номер марки материала.
Сферы применения углеродистых сталей
Углеродистые стали обыкновенного качества используют для изготовления двутавра, уголка, швеллера, прута, листа и другого проката. В производстве инструментов и деталей для разных областей машиностроения применяют углеродистую сталь высокого качества.
Источник